- News
- Fenestration Interfaces: The Devil is in the Detailing
August 4, 2017
Fenestration Interfaces: The Devil is in the Detailing
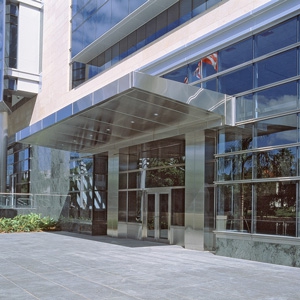
At the Southeast Region Spring Meeting, Kevin Longest and Karen Zimnicki of Wiss, Janney, Elsner (WJE) reviewed common sources of bulk rainwater penetration at and around fenestration components in building enclosures and discussed the responsibility of the architect to understand and mitigate these risks. They reviewed case studies illustrating poor interface detailing, project document discrepancies and the consequences of shifting design responsibility “downstream.” Finally, they considered the potential of Building Enclosure Commissioning (BECx) to address these concerns.
Uncontrolled rainwater penetration, condensation and moisture-related deterioration are the most common threats to the structural integrity and performance of the building enclosure. As much as 90 percent of all water intrusion problems occur within one percent of the total building area (interfaces), according to the Construction Waterproofing Handbook.
Often, the proper integration of related components of a building facade is doomed from the start because architects typically feel that exhaustive detailing is not part of their responsibility. However, this is contrary to the implication of the International Building Code (107.2.4 Exterior Wall Envelope) which states that “Construction documents…shall provide details of the exterior wall envelope as required, including flashing, intersections with dissimilar materials, corners, end details, control joints, intersections at roofs, eaves or parapets, means of drainage, water-resistive membrane and details around openings.”
Failure to provide enough information to convey how those materials and systems are reconciled at the interfaces effectively shifts the burden of designing these details to the submittal review and shop drawing phase and often results in leakage.
Longest and Zimnicki provided case studies of a shopping center, apartment building and a hotel to show how independent design review disclosed inconsistencies among drawings and made recommendations for better perimeter sealing, verified by testing. They summarized lessons learned – both from a construction process and design features standpoint, among them:
- Lack of coordination between wall flashing and doors often results in the flashings directing water behind door perimeter sealants.
- Lack of coordination of wet/dry line of typical window wall and operable vents can result in unsealed framing interfaces.
- Testing of integrated mock-ups or completed work early in construction can likely identify issues before they become building-wide problems.
- Poorly designed interface details can result in leakage during the mock-up phase. Care must be taken that information gained from mock-up is carried over to on-building construction to ensure that the as-built construction matches the design intent of revised details.
The WJE duo also covered the various aspects of BECx as related to established norms as set forth in National Institute of Building Sciences (NIBS) guidelines and ASTM BECx standards E2813 (2012) and E2947 (2016).
Commissioning helps avoid failures related to the effective management of heat/air/moisture transfer, especially considering today’s increasingly complex designs, rising energy costs and challenges to indoor air quality. It also improves long term performance, energy use, occupant comfort, safety and aesthetics, and extends the service life of the building.
The BECx process typically unfolds across the four phases of pre-design, design, bidding and negotiation, construction and occupancy.
Read more from News, Southeast Region, Events